SmartF-IT: Cyber-physical IT systems to manage the complexity of a new generation of multi-adaptive factories
Problem definition and objectives
In order to survive in international competition, companies must meet a variety of challenges. The planning and operation of multi-variant assembly systems are particularly affected by this, since influences resulting from product variants such as different components, processes and time spread must be taken into account. The result is a growing amount of effort in assembly planning, since an increasing amount of information has to be processed in increasingly shorter intervals in order to make the right decisions. In addition, changes are continuously being made to existing assembly systems. However, these changes are often not sufficiently documented and fed back into the planning process.
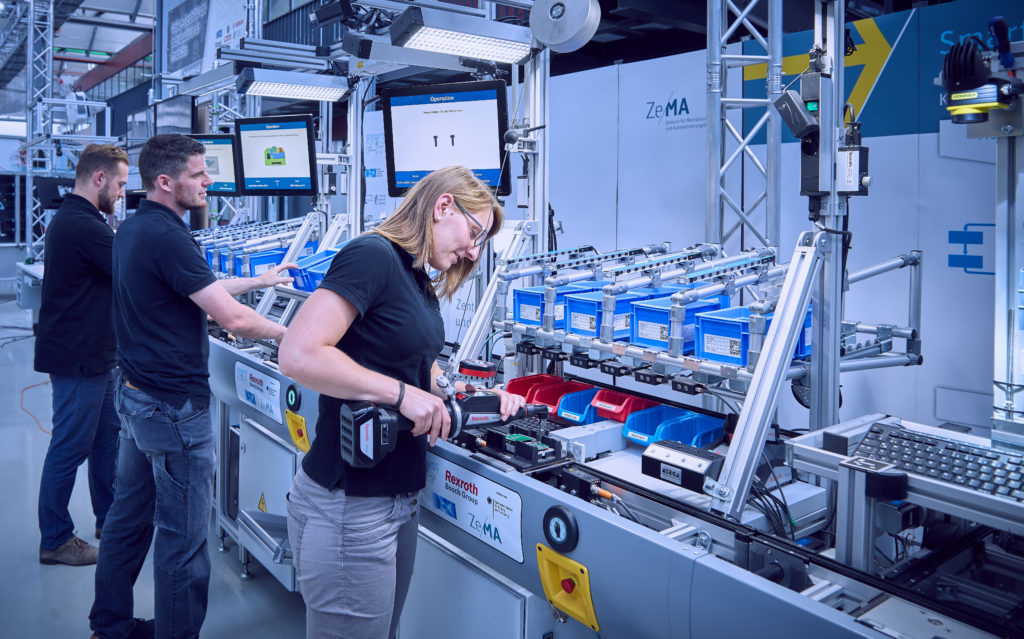
In order to meet the challenges mentioned above, the ZeMA research project SmartF-IT is investigating how digital planning tools can support employees in the planning process through targeted and consistent use of information to describe products, processes and resources. In addition, the project is investigating how this information can be transferred from the virtual world into reality so that product changes, for example, can be implemented more quickly on the assembly line. On the other hand, research is being conducted into how information about the current system configuration can be fed back into the model in order to keep the planning basis up to date.
Therefore, the following objectives are to be achieved:
- description of product, process and equipment (with regard to requirements and capabilities) in models
- Demonstrating the effects of product changes on the existing assembly system
- Consistent use of data from planning for the operation of the assembly system
- Feedback of real system conditions into the planning for continuous improvement of the results
- For validation, a close exchange with industrial partners and the construction of a cyber-physical demonstrator facility at ZeMA will take place.
Procedure
In order to support the assembly planning and a consistent networking of reality and virtuality, methods and description models are first developed. On the one hand, this involves investigating which information is required and, on the other hand, how product requirements and equipment capabilities are to be described. In accordance with the description model, the data model of the planning software is adapted, in which the effects of product changes on the assembly line are shown virtually.
For the continuous use of information, agent-based and parameterized controls are set up, which also consider the description model, as well as technical systems for the identification of the system configuration status.
Current project status and results
At the end of the project in 2016, the main focus of activity was on the consistent use of information and the return of the current mounting system configuration to the planning environment. This feedback results in an update of the model in the planning. On this basis and under consideration of the description model, new variants are verified.
The SmartF-IT demonstrator system on the P4P
The demonstrator facility will map the existing challenges of the participating industrial partners. These include the assembly of different product types and variants with batch size 1 on an assembly system as well as rapid commissioning and feedback of changes to the system by linking the real and virtual assembly world.
The demonstrator line, on which a multi-variant control unit is assembled, consists of four workstations which are interlinked by their modular design and the integrated transport system. The product is assembled in the first three stations, while rework is carried out in the fourth station. Different assembly modules are located in the individual basic modules of the plant, which are used by the worker for assembly and support him in manual activities. On the screens of the respective stations, the worker is provided with information on which assembly step is to be carried out next and which activities are to be performed. In addition, the worker is supported by various systems in the correct removal of components by displaying from which small load carrier a component is to be removed. A lightweight robot is also used to support employees during assembly. This robot can be used flexibly and temporarily for various tasks such as the handing over of components or the removal of completely assembled products.
A virtual model of the assembly system and product variants exists in the virtual planning environment. By means of a requirements/capability comparison, adjustments to the product can be secured virtually and transferred to reality via an agent-based control system. If adjustments are made to the real system, the system configuration status is identified using a methodology and transferred to the virtual environment in order to continuously update the model. As a result, the planner always has an up-to-date status for his planning, so that the information cycle between the real and virtual world is closed and thus a cyber-physical assembly system exists.
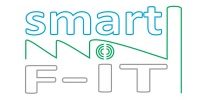
Duration: 06/2013 – 05/2016
Supported by: Bundesministerium für Bildung und Forschung